Curious How Microprocessor-Based SCR Power Controllers Can Make Your Industrial Heat Treat Process Easier?
Utilizing silicon controlled rectifier (SCR) technology makes predictive maintenance and intelligent power control possible
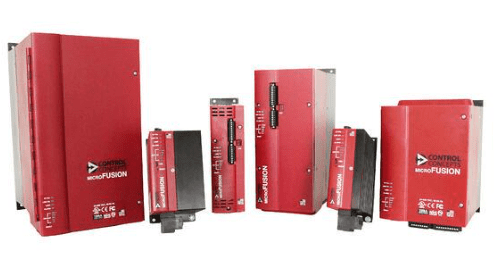
Introduction
Precise temperature regulation is undoubtedly the top variable in the industrial process that influences the quality of the final product. This is particularly true in the manufacturing of metals and in the heat treat industry. If temperature is just a few degrees off it can mean the difference between having to scrap a final product or not passing an audit.
This article addresses how Silicon Controlled Rectifiers (SCRs) have a major influence on temperature regulation, and improve the industrial heat treat process utilizing intelligent power control and predictive maintenance. SCR Power Controllers regulate the flow of electricity from the grid to a major heating element. Usually, the heating element is a furnace, kiln, or oven, and the SCR is often connected to a transformer that is connected to the heating element or the heating element itself.
The ability to calculate resistance in a furnace can provide information on the overall condition of an element. The SCR collects data and communicates back to the network. Predictive maintenance is knowing when an element has reached its useful life. This article will also define what an SCR Power Controller is, how it functions, and the different firing modes.
Digital Thyristor / SCR Power Controller Overview
“Thyristor” is a Greek-derived word for “door”. The term is a hybrid of the words thyratron and transistor. As defined by Electrical Technology, a thyratron is a gas-filled tube that works as an SCR. Both SCR and Thyristor are interchangeable terms in describing a device with four semiconductor layers or three PN junctions with a control mechanism. These small machines are known as latching devices. In the context of electrical engineering, a latch is a type of switch where once it’s ON, it will remain ON, after removing the control signal.
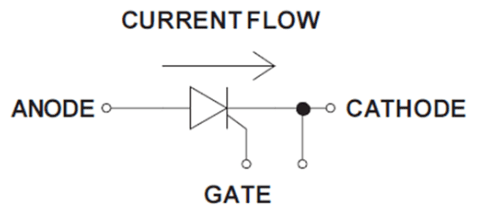
The actual power control module is an advanced electronic device with LED indicators and I/O terminals. This photo illustrates SCR power controller units attached to the side of an industrial furnace. The main internal components of an SCR power controller include:
- Semiconductor power devices (SCRs and Diodes)
- Microprocessor-based control circuits normally referred to as the firing circuit
- Heat sink (a means to dissipate the heat generated from semiconductor devices)
- Protective circuits (fuses and transient suppressors)
The below diagram is a very basic model showing one leg of an SCR controller. However, in all electrical designs of power controllers, such as the popular Control Concepts MicroFUSION series, each controlled leg requires SCRs back-to-back within the power control module because you have alternating current.
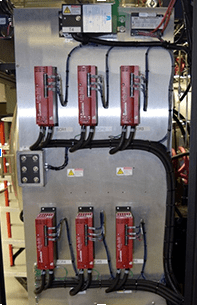
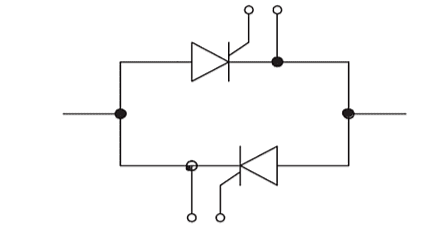
How Digital SCR Power Controllers Are Superior to Their Analog Predecessors
“Digital” SCR Power Controllers, is basically a concise way of referring to a power controller unit that utilizes an SCR switch (as opposed to a different switching method such as IGBT), and has all of the above components. Additionally, these units contain microprocessors that make them more of a smart device. They are scalable and easily paired with other digital units, whereas pairing analog power controllers results in potential emitter gain and bias.
Digital SCR Power controllers can provide flexibility unmatched by analog units. This flexibility includes various communication options, and the ability to switch through firing modes with ease. All without requiring the unit to be changed or rewired. The adaptable nature of digital SCR power controllers allows them to be incorporated into an industrial heat treat process much more effortlessly.
Older analog units are not highly configurable like their digital replacements. Newer SCRs not only have configurable faults and alarms, but also savable configuration files which can easily be loaded on another unit.
Digital SCR power controllers can obtain accuracy and repeatability not previously possible with analog controllers. Digital units have power regulation capabilities that adjust for both variations from the mains and resistance from the heating element. This form of power regulation is not only the most precise way to regulate temperature, it also allows for process repeatability.
SYNC-GUARD™ is another novel feature not previously available on older SCR controller modules. This feature is actually a trademark of the Control Concepts Inc. MicroFUSION brand of SCR power controllers. Synchronization of two units connected to the same power source, firing in zero-cross mode, is not ideal. This means that modules should not sync up so that they are on and off in unison. If this should happen, the process would require a large amount of current to be drawn from the source while the controllers are all on, and none when they are off.
The SYNC-GUARD™ feature reduces the peak current draw required from the source over time by causing each controller to attempt to find a time to turn on when fewer, or no other, controllers are firing. However, it has its limitations.
The more controllers that are added to the application, the probability of them syncing increases. Once 10 or more controllers are utilized in an application, it becomes impossible to not have some sync up despite the SYNC-GUARD™ feature.
Other key differences include digital SCR power controllers are always calibrated and are never going to change. This allows the convenience of being able to “set it and forget it.” Newer models have an option of a digital display which was previously unavailable with analog controllers.
How the Latest SCR Power Controllers Improve Industrial Furnace Operations
SCRs can calculate electrical resistance in a furnace, and provide precise power control. Intelligent power control has embedded algorithms with teach functions to calculate data and predict what is likely to happen next in the life of a heating element. This capability can determine partial load loss, resistance change, and complete load loss.
Partial load fault detection is a “watchdog” feature that monitors the system for change in resistance. This is useful for detecting an element failure for loads with multiple parallel elements. The feature reads a user set tolerance value that determines the drift from the target resistance in the system.
Therefore, an operator can enter the resistance manually or use the innovative “teach function” with a digital SCR controller. This is a form of artificial intelligence that will allow the SCR to learn the heating element through algorithms. The teach function auto-ramps and intelligently saves different resistance values at various setpoints in a process, eliminating guesswork.
Heater bakeout is an aspect of industrial furnace operations where digital SCRs offer a great amount of control. Industrial furnaces, kilns, and ovens are, more often than not, lined with some sort of refractory or ceramic material that allows them to withstand extremely high temperatures. Typically, this material can get stressed and crack if heated up too quickly, particularly in some submersion heaters where moisture can be present.
Modern SCR power controllers have an actual heater bakeout mode that will increase the temperature to the heating element gradually, allowing the furnace to slowly equalize in temperature. If any moisture it present in the heating element, it is baked away, and either way, slowly ramping up the temperature prevents damage to the refractory. This can prevent both costly furnace repairs and downtime.
Lastly, another major advantage of digital SCR controllers is tap change indication that informs the operator when to change voltage taps. Some loads, even if they remain the same, still have the ability to influence and change the element resistance over a period of time. This affects the power factor, and to compensate, a transformer with multiple voltage taps can be used. Digital SCR controllers can also be utilized to achieve a constant output power. The tap change indication feature signals to the operator when to adjust the voltage taps to a higher or lower setting on a digital display or digitally via the alarm monitor panel.
Predictive vs. Preventative Maintenance
Predictive maintenance has become a popular buzzword related to “Industry 4.0” as we now enter what is known as the fourth industrial revolution, or digitization of a manufacturing process utilizing an interconnected network of smart devices. The goal of both predictive maintenance and preventative maintenance is to increase the reliability of assets, such as an industrial furnace, oven, or kiln used in the heat treat manufacturing process. This not only avoids costly downtime, but increases the life of an asset resulting in substantial savings in maintenance costs.
The main difference between the two is preventative maintenance is simply regularly scheduled upkeep, such as a temperature uniformity survey (TUS) on an industrial furnace. You perform preventative maintenance on your vehicle when you have the oil changed every 3,000 miles because it’s common practice for extending the life of your engine.
Predictive maintenance is more condition monitoring or intelligence gathering on the health of an asset. It is based on present and continuous data monitoring from smart devices on an industrial network. Predictive maintenance is knowing when an element needs to be fixed or has reached its useful life, therefore needs to be replaced. Knowing the life of the element allows for a structured shut down preventing expensive unscheduled downtime.
How do SCRs achieve intelligent power control?
In the instance of intelligent power control, the SCR acts similar to a dimmer switch on a lighting fixture. It regulates the amount of electricity going into the furnace, just like the dimmer controls the amount of brightness to the light bulb. The purpose of regulating the electricity to the heating element is to maintain the desired temperature and prevent damage to the asset from power surges or voltage inrush.
Resistance is an electrical engineering term that relates to the amount of current that can flow through a heating element of a furnace, machine or another electronic device that heats up. Technically, this can be something as simple as your household toaster. When the heating element is cold, the resistance to electricity is lower, allowing more current to pass through. When it is hot, its resistance is higher, blocking the incoming current.
Both variations in the electricity coming from the grid, aka the mains voltage, and furnace resistance can cause temperature fluctuations. SCR Power Controllers accommodate for both variations from the mains and furnace resistance by regulating output current utilizing different firing modes.
Firing Modes of Silicon Controlled Rectifiers – Phase Angle & Zero Cross Explained
What technically is a “firing mode” when it comes to SCRs? As noted in the above diagram, the topology of an SCR includes a control circuit also known as a “firing circuit”. The SCR has feedback and logic to determine how it’s going to fire the electric sine wave. Thyristors, as they are more commonly known outside of the U.S., have two basic control modes, phase-angle, and zero cross.
Phase-angle
When an SCR power controller adjusts the voltage using the firing angle, it is known as phase-angle mode. This is analogous to a dimmer switch on a light fixture. The SCR is acting as a dimmer switch on an industrial furnace. Using phase-angle control, each SCR in a back-to-back pair is turned on for a variable portion of the half-cycle that it conducts. This trims every single half sine-wave, giving a very smooth output, hence getting the correct kilowatts to the needed load.
In a heat treat application where the SCR is firing directly into the transformer, phase-angle mode will need to be employed. This protects the transformer from saturating.
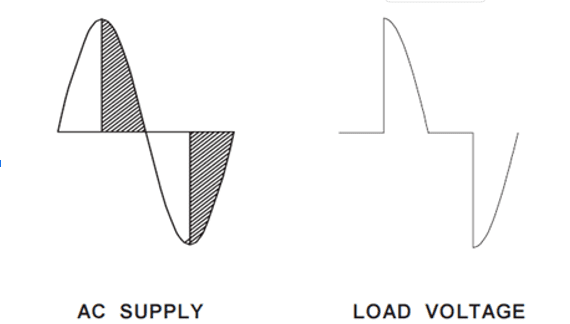
Zero-Cross
In zero-cross firing mode, the power controller adjusts the duty cycle to regulate the voltage. Each SCR is turned on or off only when the instantaneous sinusoidal waveform is zero. In zero-cross operation, power is applied for a number of continuous half-cycles, and then removed for a number of half-cycles, to achieve the desired load power.
In other words, zero-cross is best described as blinking on and off. You’re firing a certain amount of full-wave cycles, then it’s going to turn off for a period of time, and then return to the on mode. An average is taken of the cycles that fire verses don’t fire, which gives you control.
The on and off nature of zero-cross is beneficial for power factor, and the overall cost is lower than running SCRs in phase- angle applications. Simply stated, running SCRs power controllers in zero cross mode versus phase angle mode, consumes less energy. Therefore, saving money on the electric bill. Zero-cross also produces little to no harmonics. As illustrated below, you can run SCRs in two-phase versus three-phase mode using zero-cross. If the resistance is varying less than 10%, zero-cross can be applied to the heat treat process.
SCR Power Controller Configurations
Single-Phase
In a single-phase configuration, SCRs are running back-to-back to the load, which is looping back up to L1 and L2. This is the most basic SCR setup.
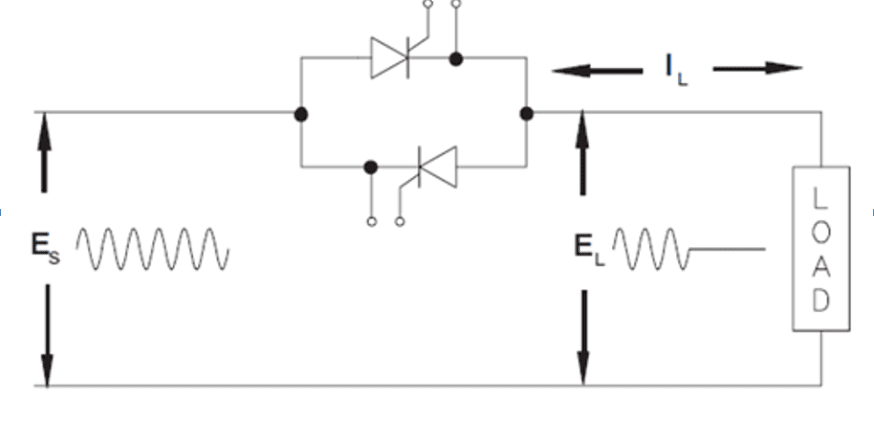
Three-phase / 3-leg (6SCR)
Three-phase is wired in a delta or wye and involves three SCRs modules connected together in a circuit. This is great for phase-angle control where the SCR is firing into transformers. The topology is beneficial for direct firing as well. It’s used for high inrush current loads where a current limit really needs to be applied and being able to phase without blinking on and off.
Three-Phase SCRThree-phase / 2-leg (4SCR) Zero-Cross Only
This configuration involves two SCR modules controlling two of the legs, and the third leg is connected to the delta or wye, but goes directly back to supply voltage. This can be more cost-effective for an application since it’s run in zero-cross mode.
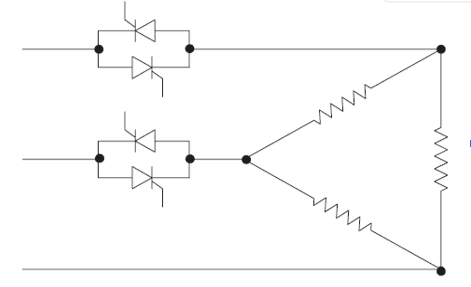
Inside Delta
Inside Delta configuration is double the wiring. However, it reduces the size of the SCRs needed because where the SCRs are placed in the circuit, it’s going to draw less current at the point. This is a more uncommon configuration but seen out in the field in some instances.
What SCR is right for your application?
At Weiss Industrial, we chose to partner with the “best in class OEMs” to help provide our customers with uninterrupted and efficient plant operations. We teamed up Control Concepts Inc. (CCI) on their MicroFUSION SCRs power controllers because we found their product to be the most reliable, and they have superior customer service. Control Concepts power controllers are manufactured in the USA from their 54,000 square foot, company-owned facility in Chanhassen, MN.
Tony Busch, Sales Application Engineer, notes that one of the bigger factors to consider in selecting the right SCR power controller is the load type. Some loads require zero-cross firing modes, others phase-angle only, and in certain cases, it doesn’t matter. It can either be zero-cross or phase angle.
The main rule of thumb is to never use zero-cross on fast responding loads, such as usually infrared lamps and low mass heaters. In this instance, zero-cross will cause too much of an inrush current and can burst lamps and/or fuses down the line. On the other hand, loads in which the resistance changes are less than 10%, such as nickel and iron-chromium, zero-cross must be used. Operators also prefer zero-cross in instances where low harmonics are required, as it produces fewer harmonics than phase-angle firing mode.
CCI has created a 10 question PDF guide about your industrial process that will help you select the right SCR power controller for your application. You can download the “Questionnaire for Selecting MicroFUSION” here.
Conclusion
In conclusion, SCRs can be an integral part of an industrial network that improves the modern heat treat manufacturing process by providing precise, intelligent power control. They also achieve predictive maintenance not previously possible by their analog predecessors. Their advantages are numerous in improving industrial furnace operations and the heat treat manufacturing process.
Other major advantages of SCRs are their high reliability. Since they are solid-state devices, there is no inherent wear-out mode that can be associated with other industrial mechanical machinery that has gears or moving parts. This means little to no maintenance of the SCR Power Controller.
They have infinite resolution, which means if there is an incoming supply voltage of 480 volts, sequentially, 480 volts will be returned from SCR when it is on fully. There’s no trim back or load losses involved. You can go from zero to 100% if you want to control your voltage, power or current.
SCRs also have an extremely fast response time, which allows the operator to turn the device on and off very quickly. Mostly in North America, you are running voltage on 60hz at 120 half-cycles per second. SCRs allow you to target a particular half cycle, and turn it on and off very quickly. This is a great feature for loads that have high inrush current, acting as a soft starter, to keep from saturating the heating element.
Want to learn more? Weiss Industrial has partnered with Control Concepts to produce a PDF document entitled, “A Guide to Intelligent Power Control & Temperature Regulation Utilizing SCR Technology”, which you can download here.
About the Authors
Tony Bush – Control Concepts Inc. (CCI)
Sales Applications Engineer
Tony is a graduate from Dunwoody College of Technology, in Minneapolis, MN, with a degree in Electrical Construction. He started his career at the Control Concepts Inc. headquarters in Chanhassen, MN, as test technician, quickly transitioning to field service and repairs. In 2014, he began his current position as a Sales Application Engineer and became Bussmann SCCR training certified. What Tony loves most about his job are the opportunities it has given him to travel throughout the US as well as internationally to visit SCR applications in Denmark, France, India, South Korea, Taiwan & China.
Meredith Barrett – Weiss Industrial
Marketing and Business Development Manager
Meredith has a Communications degree from Penn State University, and over 20 years of experience in sales, corporate communications, marketing and business development. Her experience in the industrial sector and manufacturing began in 2014 when she took on marketing and lead generation contract role the for Medium Voltage Drives division of Siemens Industry. Meredith joined Weiss Industrial, a manufacturers’ representative company, in January of 2020 to assist in building a new marketing department and lead generation program, while also supporting business development.
About Weiss Industrial
Weiss Industrial is a small business that serves very big industries. Our story begins in 1965 when Elek K.Weiss founded “Weiss Instrument” in Pittsburgh, PA, as an Engineering Representative firm. Pennsylvania, and its surrounding states, continue to be conducive to the success of a company centered around industry. The company was purchased in 2018, by the current owner and former Marine, Tony Luciana. We are proud to be a veteran-owned company, and have many veterans on our team.
Our company slogan is “the equipment and services to keep you running.” Weiss Industrial is the contracted outside sales channel for 13 industrial OEMs. Combined, our sales team of eight individuals has 250 + years of field experience. We serve manufacturers and utilities across various industries including steel, oil & gas, power generation, glass, and industrial heating – just to name a few.
Weiss also has a team of dedicated service technicians available on dispatch from our Pittsburgh office to perform onsite calibrations, temperature uniformity surveys and UPS maintenance checks. Additionally, we have an in-house calibration laboratory. You can view our full-service offerings here. Weiss Industrial in ISO 17025 accredited services provider.